Parts and contents of a Safety Case
Safety Case is composed of a set of documentary evidence divided into six main parts:
- The Definition of the System under analysis.
- The report on quality management.
- The report on safety management.
- Technical Safety Report
- References to Safety Reports.
- Conclusions.
Initially, in the definition of systems under analysis (Section 1), it is important to specify precisely the system, the equipment or the subsystem under monitoring of the safety case, giving shape to the equipment: application boundaries of the equipment, that is, as far as it goes, therefore, by correctly defining the interfaces with the rest of the systems with which it coexists. It is also very important in a safety study to define the versions (and edition) of the equipment and subsystems that make it up and that apply this safety case.
The report on quality management (Section 2) is considered the first condition that a project -executed by a company- must meet, and evidence shall be given that quality is controlled by an appropriate quality management system. Typically, this report presents a mix between compliance with ISO9001 at the generic quality level and compliance with EN 50126 in terms of RAMS life cycle.
Safety Management Report (Section 3) is responsible for providing evidence that safety is controlled by an appropriate security management system, being consistent with RAMS Management process described in EN 50126. In summary, this report will provide evidence regarding:
- V-model product development life cycle has been followed according to EN 50126 standard.
- An organization is available with an adequate level of independence -between management, design and validation/ verification- and with an appropriate competent level -in terms of knowledge about personnel involved in the project-.
- A risks record called Hazard Log.
- The specification of safety requirements.
- In-house system design where the system design has been documented by any objective standards: mechanical, electronic, chemical, optical, software, communications, etc.
- Verifying and validating safety targets.
Technical Safety Report (Section 4) must contain the technical principles that ensure design safety, including detailed technical specification, design calculations, results of type tests, etc. To sum up:
- Introduction.
- Guarantee of proper operation.
- Damage effects.
- Operation under external influences.
- Application conditions (safety relations).
- Test results.
In References to Safety Reports (Section 5), other Safety Reports depending on the Safety Report being under analysis must be referenced. This documentation for complex Safety Cases occurs in cases where, for some reason, some sort of dependency is of interest regarding another product, system, sub-system, which has been already previously certified.
Finally, in Conclusions (Section 6), the set of evidence presented in the previous Sections should be summarized, arguing that the "system is sufficiently safe according to the specified application conditions".
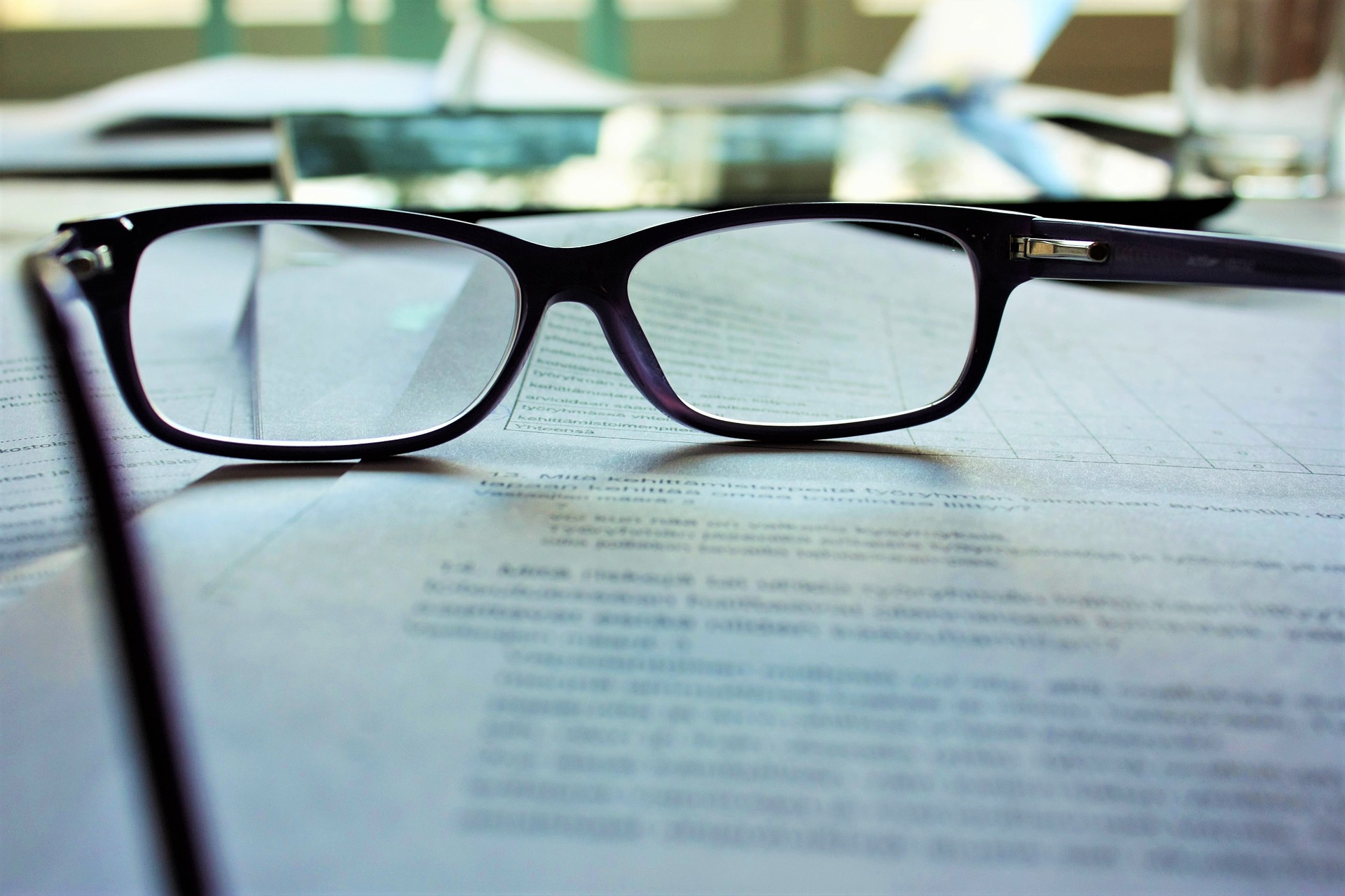
At Leedeo Engineering, we are specialists in the development of RAMS Railway projects, applying CENELEC standards EN 50126, EN 50129, EN 50128, EU Implementation Regulation 402/2013 with the application of the Common Safety Methods CSM-RA, supporting any level required to RAM and Safety tasks, in the development and certification of safety products and applications.
Are you interested in our articles about RAMS engineering and Technology?
Sign up for our newsletter and we will keep you informed of the publication of new articles.