Los métodos para evaluar la fiabilidad de un sistema
La Ingeniería RAMS permite mediante diferentes técnicas calcular la fiabilidad de un producto, sistema o instalación. Es importante empezar este artículo explicando que saber la fiabilidad de un equipo acostumbra a no ser tarea fácil ya que nos ponemos como objetivo, en muchos ocasiones, predecir cuándo un equipo fallará: Introduciendo un poco de humor al asunto ¿desde cuándo ha sido fácil predecir el futuro? A esto se le añade, acorde a nuestra experiencia, un punto de partida con información escasa, tiempos cortos de experimentación y poco conocimiento de la tecnología bajo análisis, lo que dificulta en toda regla, los procesos de evaluación de la fiabilidad.
Existen diversas maneras de afrontar el cálculo de la fiabilidad o tasa de fallo de un equipo. En este artículo presentaremos las estrategias más utilizadas a día de hoy por sectores de referencia de la Ingeniería RAMS como la Ferroviaria o Aeronáutica.
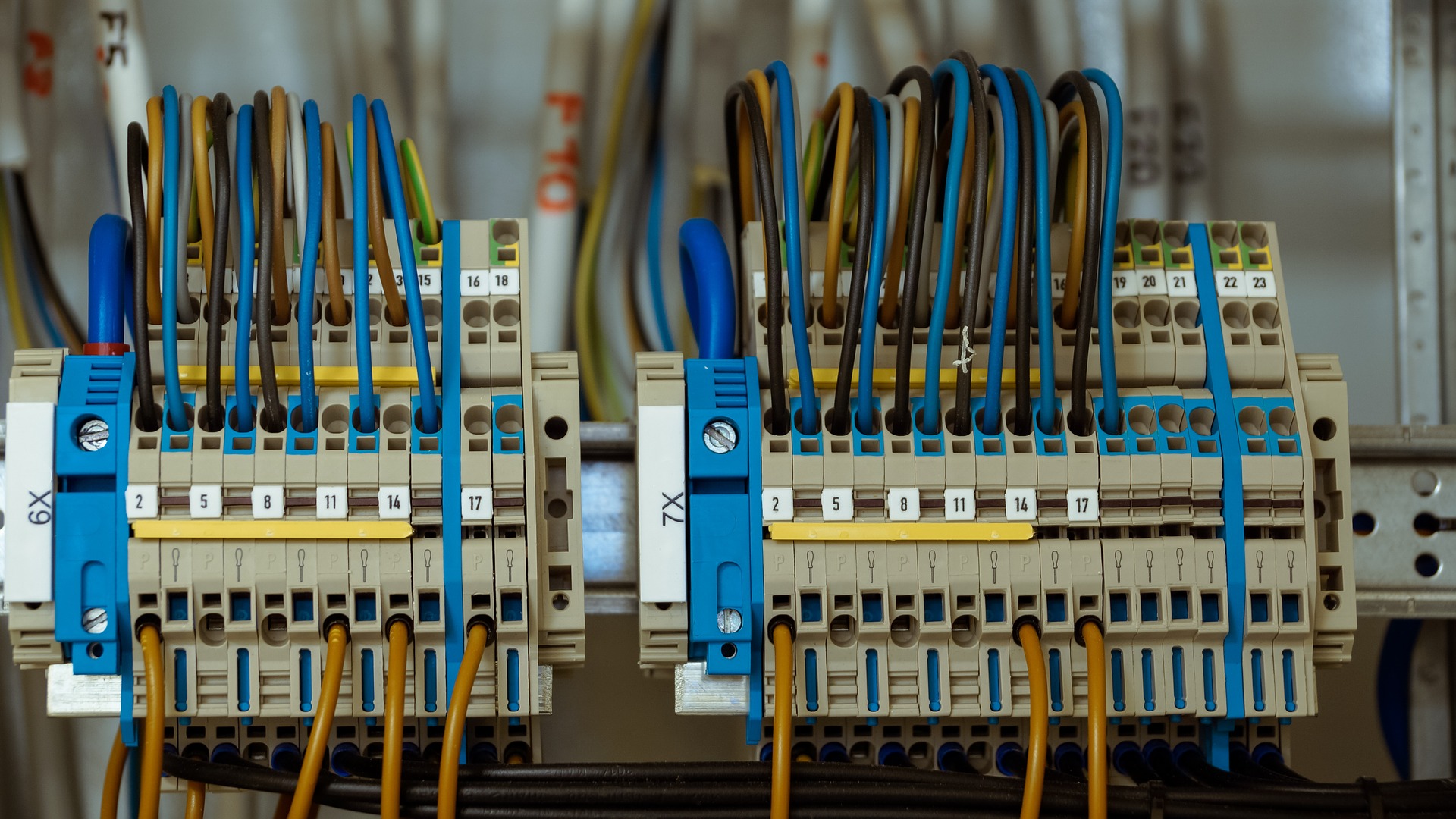
Recomendamos la lectura de los siguientes artículos si no
estás familiarizado con los conceptos básicos de la fiabilidad y los
parámetros RAMS:
Lo primero que es importante explicar es que el cálculo de la fiabilidad no es un parámetro determinista. La fiabilidad debe ser entendida como un parámetro probabilístico que intenta predecir de qué manera fallará un equipo en el futuro. Por tanto, estrictamente la fiabilidad no puede medirse con exactitud y de forma repetitiva.
La definición básica y clásica de la fiabilidad es de la probabilidad de proporcionar un nivel de funcionamiento especificado durante un tiempo especificado en un ambiente especificado.
Además, la evaluación de la fiabilidad, en muchas ocasiones, debe tener por objetivo identificar y entender los principales contribuyentes a fallo de nuestro sistema, más que la propia exactitud del cálculo de cuando fallará nuestro equipo. Esta identificación nos permite establecer de forma priorizada planes de acción inteligentes y respaldados por datos cuantitativos, de la mejora de los parámetros o indicadores RAMS de nuestro sistema.
Además, entenderemos o interpretaremos la fiabilidad de dos maneras distintas dependiendo si hablamos de un equipo independiente como un tren, una instalación ferroviaria o, si hablamos de una fiabilidad asociada o relacionada con la población de un producto y, en donde el producto se caracteriza por tener un volumen de producción o implantación elevado. Veamos un ejemplo: Imaginemos un producto con valor de fiabilidad "tiempo medio entre fallos" MTBF, de 1.000.000h y una implantación de 1.000.0000 de estos productos en una instalación. Esta MTBF tan alta no significa que el producto vaya a durar 1.000.000 horas en funcionamiento antes de fallar, es decir, 114 años. Más bien significa que, a nivel promedio y de forma estadística, fallará uno de estos productos cada hora en nuestra instalación (1 millón de hora con una población de 1 millón de equipos). Por tanto, lo que parecía un valor muy bueno de fiabilidad, en realidad, poniéndola en contexto, no lo es tanto.
¿Cuándo es necesario llevar a cabo una evaluación de la fiabilidad?
Típicamente en Leedeo Engineering, desarrollamos cálculos de la fiabilidad de un producto o sistema para cumplir con uno de estos objetivos de nuestros clientes:
- Cumplimiento de los objetivos de fiabilidad o disponibilidad requeridos en los sistemas. Por tanto, el cumplimiento de los requisitos en cuanto a la fiabilidad o disponibilidad.
- Selección del mejor diseño. Evaluación de la mejor implementación de una solución cuando se tienen diferentes alternativas para solución una necesidad.
- Priorización de mejoras del producto. Como hemos comentado anteriormente, el conocimiento de los puntos de infiabilidad de un sistema, permite priorizar mejoras en el sistema con base a datos empíricos, descartando intuiciones, olfatos o situaciones de operativa poco claras y concisas.
- Soporte Logístico Integrado. Repuestos, estrategia de las garantías que se le otorga al cliente que compra el producto o sistema, cálculos de LCC (costes de ciclo de vida). En este punto también introducimos la previsión del tipo de actividades de mantenimiento que deberán hacerse.
Método 1 para la estimación de la fiabilidad: análisis por similitud
El análisis por similitud utiliza datos fiables (valga la redundancia) de funcionamiento del equipo en explotación para comparar el nuevo equipo diseñado con el equipo predecesor y así estimar la fiabilidad del producto evolucionado. Como se puede observar este método nos sirve para evoluciones de producto, en productos que tenemos en servicio y con muchos de experiencias y, en los cuales, por la necesidad que sea, se decide evolucionar a un producto mejorado o con unas características nuevas. Siendo capaces de identificar la parte del diseño que es igual y la parte del diseño que es diferente a la anterior versión, seremos capaces de apalancar la información del anterior producto a la parte diseño igual.
En este método entra en juego el concepto de las lecciones aprendidas y el retorno de la experiencia. Muchas empresas evolucionan sus productos y empiezan un análisis de fiabilidad sin tener en cuenta que quizás el 80% del producto lleva "testeándose" en el producto anterior durante los últimos 20 años. Consideramos que es imperativo, frente a esta situación, utilizar la experiencia que nos ha aportado instalaciones y equipos anteriores.
En este concepto de análisis por similitud, se puede ver la importancia del diseño por bloques o modular. Si hacemos un diseño e incluso una fabricación, en bloques de forma modular y, reaprovechamos módulos en diseños próximos, conseguiremos tener información de cada uno de los bloques, que fiabilidad tienen y como fallan. Si no tenemos un diseño modular, al empezar un diseño nuevo, no es obvio partir de de otros proyectos, diseños o productos, información sobre la fiabilidad de sus sub-componentes. Por tanto, de nuevo, tenemos otra variable que sustenta un diseño ordenado, organizado, modular y con una estrategia de integración paso a paso, típico de un diseño de ingeniería V-model.
El análisis por similitud también debe contener los elementos no sólo propios del equipo sino también los elementos exógenos al mismo. En este sentido, dichos elementos también deben coincidir para apalancar la experiencia de instalaciones y servicios previos: temperatura y choques térmicos, humedad, estrés mecánico, ciclos de trabajo, etc.
Método 2 para la estimación de la fiabilidad: análisis de durabilidad
La evaluación de la durabilidad se usa para estimar el tiempo que tarda un sistema hasta fallar, mediante la ejecución ensayos, definiéndose como el análisis estructurado de la respuesta de un elemento del equipo al esfuerzo resultante de la operación, mantenimiento, transporte, almacenamiento y otras actividades a lo largo del ciclo de vida.
Es habitual, para esta estrategia, utilizar métodos de ensayos acelerados, que permiten, aumentando el stress del equipo bajo test, poder multiplicar el tiempo efectivo versus el tiempo real del ensayo. Las variables típicas a valorar en este tipo de ensayos son, los esfuerzos térmicos, climáticos, mecánicos y eléctricos. Esto es especialmente útil cuando queremos introducir en el mercado o, poner en servicio, un equipo sin requerir que antes esté en pruebas un tiempo como mínimo igual al su tiempo de vida esperado, situación la cual acostumbra a suceder siempre. Para la mayoría de industrias no es posible esperar, debido a las necesidades del time to market, a introducir un producto al mercado un tiempo igual a su tiempo de vida esperado.
Los ensayos acelerados nos permiten por tanto, en pocos días o semanas, llevar al equipo a un desgaste y uso equivalente de años y, por tanto, entender de qué manera se degrada y cuáles son los primeros sub-componentes o elementos que fallan. Este proceso permite la mejora iterativa del sistema bajo análisis ya que al detectar "el punto o puntos débiles" del equipo, puede mejorase ya no siendo estos puntos débiles y, volver a lanzar un ensayo acelerado de nuevo hasta detectar, el siguiente punto débil del equipo.
A parte de los ensayos acelerados, también es habitual utilizar la estrategia ensayos de tipo escalonado. Los ensayos escalonados implica aumentar poco a poco y de forma gradual, viendo la respuesta del equipo bajo análisis, las condiciones en las que funciona el sistema (de nuevo mediante variables de esfuerzos térmicos, climáticos, mecánicos y eléctricos), llevándolo, paso a paso, fuera de las condiciones de funcionamiento del equipo y, por tanto, estresando el sistema fuera de su rango de funcionamiento, para analizar cuáles son los fallos que se producen, pudiendo de este modo, entender las partes más débiles del diseño y, pudiendo, de este modo, mejorar la fiabilidad del equipo, mejorando estas partes.
Método 3 para la estimación de la fiabilidad: predicciones teóricas
La estimación de la fiabilidad teórica se basa en el uso de la información, típicamente, aportada por los fabricantes de los componentes que adquirimos y usamos, los cuales, anteriormente, han llevado a cabo en la mayoría de las veces una estimación de fiabilidad basada en el Método 1 o Método 2. Por tanto, el Método 3 de la predicción teórica, en sí, depende de alguno de los anteriores métodos.
Para este método, normalmente deberemos consultar o buscar en las hojas de datos de nuestros componentes, los valores MTTF o MTBF del componente que compramos. Otras veces, estos valores no serán fijos sino que serán factor de variables de trabajo del equipo y, el proveedor nos lo puede presentar en forma de ecuación matemática la cual modeliza el comportamiento de la fiabilidad en función de una variables.
Os dejamos a continuación un link donde veréis como una fabricante de primera línea de condensadores, aporta la información de la MTBF de sus componentes:
https://www.vishay.com/dt/capacitors/tantalum-reliability-calculator-list/
Y en el siguiente link, la información de un fabricante de pequeños motores paso a paso:
https://www.moonsindustries.com/series/nema-17-standard-hybrid-stepper-motors-b020105
Una vez tengamos la información de la fiabilidad de nuestros componentes, será posible llevar a cabo el análisis teórico de los mismos aplicando alguna de las estrategias conocidas, típicamente un Reliability Block Diagram (RBD).
Leedeo Engineering es especialista en el desarrollo de cálculos de fiabilidad de productos, sistemas e instalaciones. Con el mejor software de soporte del mercado, tenemos experiencia dentro de la industria ferroviaria, aeronáutica, de automoción, defensa y energía. No dude en contactar con nosotros si necesita llevar a cabo el cálculo de la fiabilidad de alguno de sus equipos o instalaciones.
Desde nuestras oficinas de Barcelona y Madrid, damos servicio a proyectos en España, Europa, África, Oriente Medio, Estados Unidos, Ásia y de toda América Latina (México, Chile, Colombia, Perú, etc.). Contacte con nosotros >>
¿Te interesan nuestros artículos sobre Ingeniería RAMS y Tecnología?
Inscríbete en nuestra newsletter y te mantendremos informado de la publicación de nuevos artículos.