Maintenance and risk management
Introduction
Maintenance is a term used to describe all the activities that must be carried out to keep a system fit for service, so that railway assets (rolling stock, signaling, electrification and infrastructure) remain safe and reliable throughout the life of the railway. phase of the operating life cycle.
This means that when we talk about railway maintenance we are including activities such as:
- maintenance, inspection and repetitive tests of assets;
- troubleshooting and repair;
- component replacement;
- homogeneous renovation.
Maintenance is often concerned with periodically securing some design parameters. Let's take a typical example: the distance between the rails, within the specified limits.
It may be that these limits are specified in standards or regulations. Alternatively, it may be that some organization, either in the design phase or the maintainer itself, has specified the limits to meet the security, performance and reliability objectives. In any case, allowing the parameter to go outside its limits can carry a risk and therefore must be controlled.
Within the maintenance we must also include the planning and maintenance (forgive the redundancy) of records for maintenance, which include:
- plan and record how new and modified assets will be maintained;
- planning and recording of changes to existing maintenance activities.
The boundary between what is described as maintenance and what constitutes a renovation project is not always clear. Maintenance sometimes also includes remodeling and overhaul, system modifications (temporary or permanent), and system upgrades.
Maintenance and risk management on the railway
We can say that a large percentage of railway equipment has the potential to affect safety and therefore risk control is an integral part of almost all railway maintenance. Maintenance can contribute to risks both through action and inaction, understanding risk as the level of probability of an accident occurring and the damage produced affecting the assets or people who come into contact with the system.
Having the risks, and therefore, the security under control is closely linked to the availability (performance) of the system, which is typically the variable to which maintenance is associated. A clear example from the railway world is the degraded modes when an asset fails. These allow to give availability to the system but also security since there is a path designed against a failure and the system is not derived towards unknown states that could lead to unsafe situations.
We find it important to establish systematic processes that can be used to ensure that maintenance activities are risk-focused. Normally, we will also consider risks beyond security, that is, the risk of lack of availability
Maintenance strategies must be generated based on the details of the characteristics of the failure under review, the risks that could be involved and the costs incurred.
The basic information about the selected asset in its operating context that should be taken into account is:
- the functions and associated performance standards of the asset;
- the ways in which it may fail to perform its duties;
- the causes of each functional failure;
- what happens when each fault occurs;
- the consequences of each functional failure;
- what can be done to prevent each failure;
- what to do if no suitable preventative task can be found.
A great strength of this approach is the way it provides simple, precise and easily understood criteria for deciding which preventive tasks (if any) are technically feasible and worth performing in any given operational context. It also provides a means of deciding how often each task should be performed and by whom.
Maintenance can also be seen as an activity to reduce and thus improve risk acceptance. If as maintainers we propose additional maintenance tasks (even surely at a higher cost) but reduce the risks, the railway administration can "turn the screw" in accepting risks and, therefore, make a railway system safer. In this way, we can affirm that risk acceptance and maintenance strategies and plans have a great correlation the phases with exploitation.
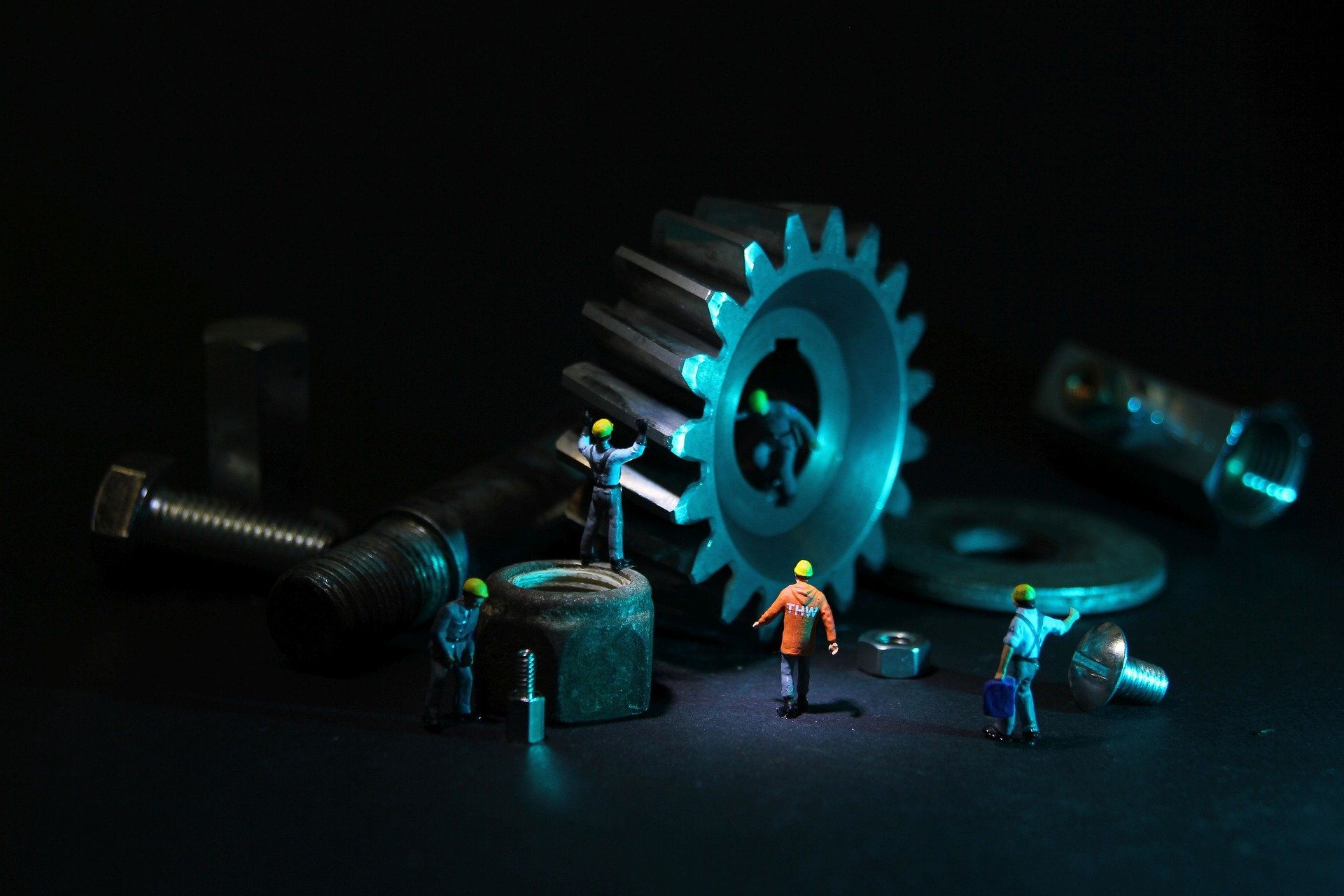
Where projects affect operational in-service rail assets (for example undergoing renovation works), new hazards may be introduced. Responsibilities for asset maintenance, including changes to how maintenance work will be performed, should be agreed between the project and the maintaining organizations before project work begins. Maintenance requirements must be fully understood and all necessary resources must be put in place to implement them.
Before changes to the railway are brought into service, project and maintenance organizations will need to agree and ensure that all necessary resources for operational safety are in place. Resources may include:
- new or improved maintenance facilities;
- additional maintenance tools and test equipment;
- replacement parts;
- new and changed maintenance standards and procedures;
- changes in staff competency;
- organizational changes;
- system configuration logs.
If only part of the rail system is being maintained, it is important to understand that changes occurring elsewhere can affect the part of the rail for which you are responsible. Therefore, it is good practice for maintainer organizations to work transversal in areas where the work could result in increased risk. For example, deterioration of the track bed may result in a higher rate of deterioration of the rolling stock suspension and vice versa.
Maintaining also implies the will to anticipate
You need to understand how the part of the railway you are maintaining degrades over the life cycle. To do this, you'll need to understand what critical failure modes exist, particularly those where the failure of a single item could lead to a significant incident. Therefore, be clear about component failures and abnormal component loads due to a failure somewhere else on the track.
On the other hand, we also recommend doing a reverse process to the previous one and analyzing variables that allow us to measure our performance as maintainers against the real performance of the railway and compare it with the performance that was predicted "the day before" starting maintenance activities. If there is a difference, it could be because:
- the assumptions, dependencies, and caveats used as the basis for making maintenance decisions were inappropriate;
- equipment design is not robust enough; or
- not all risks were adequately identified or controlled.
In Leedeo Engineering , we are specialists in the development of maintenance and maintainability plans from the point of view rigurous of RAMS Engineering and risk management, supporting our clients throughout their product development life cycle.
Are you interested in our articles about RAMS engineering and Technology?
Sign up for our newsletter and we will keep you informed of the publication of new articles.