IEC 60300-1: 2014 (UNE-EN 60300-1: 2015): Holistic Reliability Management
Reliability within the framework of IEC 60300 is defined as
the ability of a product, system, process or service to function as and when
required. It is the term used to describe the time-dependent
characteristics of an element. These systems or products may involve
hardware, software or human aspects or any integration thereof in any way.
At Leedeo we are experts in RAM and reliability methodologies and in this article we highlight the most important points of the main parts that make up the IEC 60300 and its main parts.
The IEC 60300 standard establishes a holistic reliability management framework for any type of product, system, process or service that requires specific aspects or objectives such as reliability, availability, maintainability, recoverability and durability (life cycle, LCC) which are characteristics of the reliability of a technological system.
The approach of the standard is primarily intended for technological applications and their related processes. Such technology applications, systems or products are referred to as "elements". However, reliability management can be applied in the same systematic way to non-technological applications.
The standard is organized into several parts that are listed in the following images and briefly described.
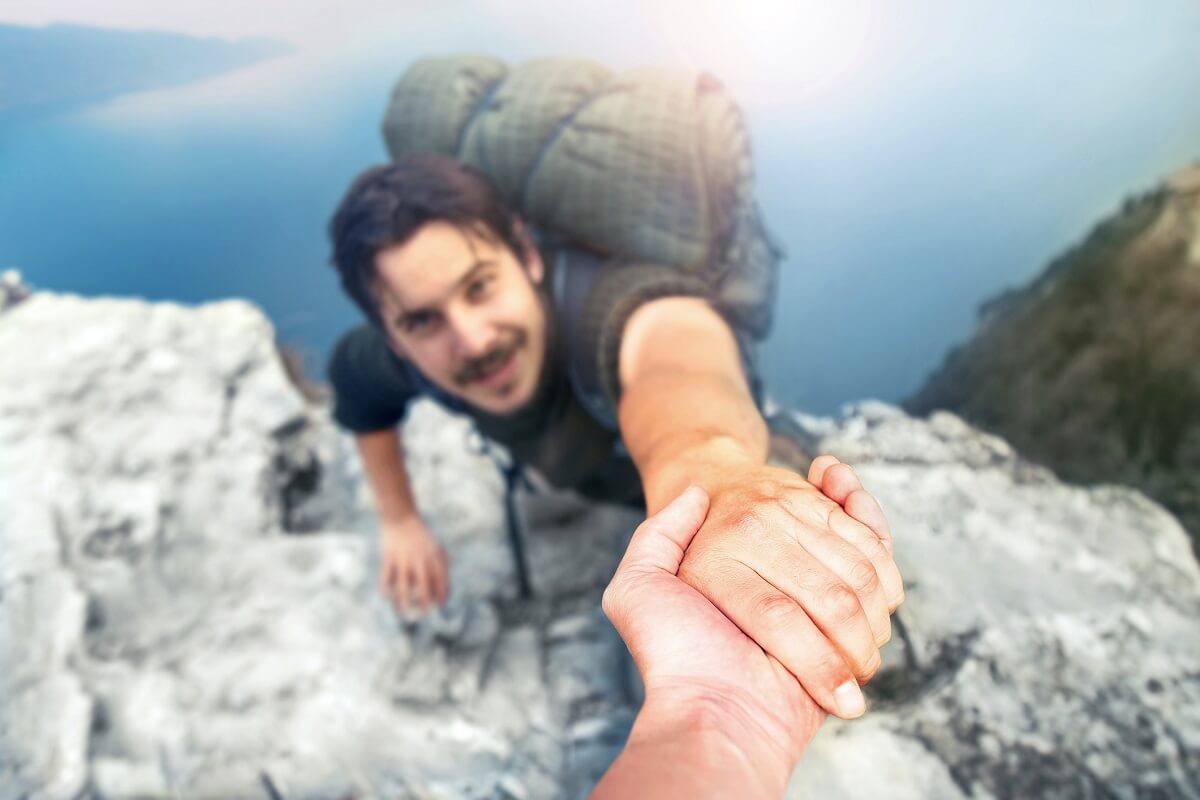
From Leedeo we highlight the following points as the
benefits of using the IEC 60300-1: 2014 standard (UNE-EN 60300-1:
2015) as well as its other parts:
- It is the standard par excellence for the application of the concepts of reliability, availability, maintainability, recoverability and durability, especially in technological applications.
- It offers a wide range of very useful techniques, analysis and methodology for managing the concepts mentioned in the previous point.
- Includes a detailed guide to conducting LCC studies
- It is used for the development of elements of Software, Hardware, Processes in which Humans intervene.

Reliability is the term used to describe the time-dependent characteristics of an element, usually of technological application.
Introduction
Introduction to IEC 60300-1: 2014 (UNE-EN 60300-1: 2015) : Reliability management. Part 1: Guidelines for its management and application.
Standard overview part 1 provides the reader with how to use the same standard, as well as the recommended and most used tools that I may need in reliability management. Useful techniques and tools are recommended to find flaws in the design phase such as HAZOP , AMFEC (FMECA) or FTA explained in other LEEDEO articles.
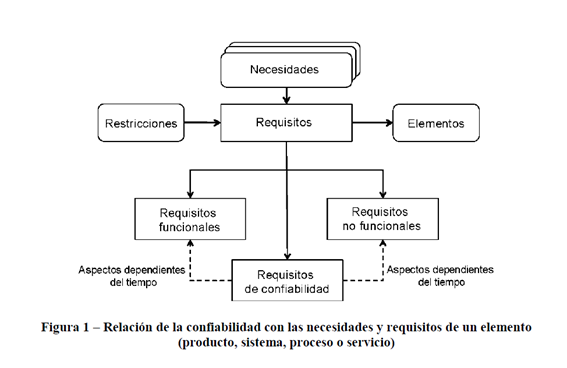
For the correct design of an element (product, system, process or service), the engineering departments of a company must take into account, especially in the initial phases of the life cycle, that the following categories of requirements must be taken into account:
- Functional requirements
- Non-functional requirements
- Reliability requirements
The correct development of all the categories of requirements listed above for the design of the aforementioned element is vital for the proper functioning of the project. By including reliability requirements from the beginning of the element design, we provide much higher reliability to both the design and the final product, always saving time and redesign. In the same way, the quality of the product is greatly improved.
This part of the Reliability standard also defines and describes the Reliability Activities within the Generic Life Cycle Phases shown below:
- Conception : in the conception phase of the element, among other project-specific tasks and not strictly speaking reliability, the preliminary requirements of the element's reliability should be defined as well as creating a reliability plan for the entire life cycle.
- Development : During project development, probabilistic approaches and detailed modeling can already be developed to obtain item reliability predictions. In this way the first checks of compliance with the reliability requirements can be carried out.
- Realization : during the realization phase of the project, no concrete reliability activities are highlighted, but many others closely related must be carried out, such as the implications of the implementations of the make-buy decisions .
- Utilization: during the utilization phase, records should be kept up to date on the status of the elements or subsystems of the elements, failure reports, etc., to ensure and also estimate the fulfillment of the reliability objectives of the element's service. It may be necessary to re-evaluate the risks and reliability requirements since during operation and maintenance the conditions of the element are in many cases changing.
- Improvement: during the improvement phase, the element can be modified to increase its efficiency, improve its maintenance or extend the useful life of the same element. These improvements must be analyzed from the point of view of reliability and therefore apply again the realization of probabilistic approaches and modeling of the reliability aspects to evaluate the impact of the improvements.
- Withdrawal: in this phase the removal of the element from the services it provides is proposed and its cutting can be planned for reuse of materials, its disassembly for reuse of certain subsystems in other uses or, in some cases, its abandonment in situ.
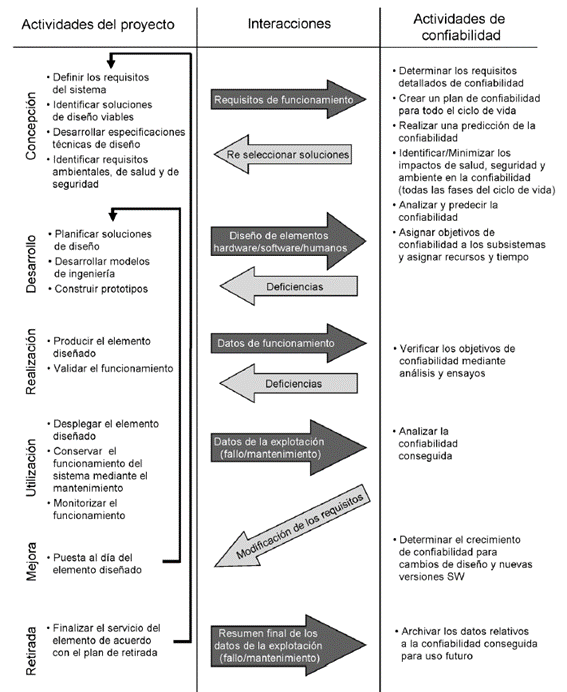
Generic Life Cycle Phase Variations
- SOFTWARE LIFE CYCLE: conception, development, application, operation and maintenance, improvement, retirement.
- PRODUCT LIFE CYCLE : Conception and definition, design and development, manufacturing and installation, operation and maintenance, improvement during useful life and withdrawal from service and disposal.
- LIFE CYCLE OF AN INSTALLATION : Conception and definition, design and development, construction and commissioning, operation and maintenance, improvement during the useful life, withdrawal from service and disposal.
- HARDWARE LIFE CYCLE : conception, design, manufacture, installation / commissioning, operation / maintenance, modification, disposal.
IEC 60300-3-1: 2003 (UNE-EN 60300-3-1: 2005): Reliability management. Part 3-1: Application Guide. Reliability analysis techniques. Methodological guide.
This part of the standard describes the uses and main applications of the different analysis techniques and methodologies for better reliability management. The main techniques that must be known to strengthen reliability management are listed below:
- Prediction of failure rate
- Failure Tree Analysis (AAF or FTA )
- Event Tree Analysis (AAS)
- Reliability Block Diagram Analysis (DBF or RBD in English)
- Petri Nets Analysis
- AMFE or AMFEC (Analysis of failure modes and their effects or FMECA in English)
- Hazard and operability studies ( HAZOP )
- Human Reliability Analysis ( HRA )
- Stress-resistance analysis
- Truth Table ( MTV )
- Statistical methods of reliability
IEC 60300-3-2: 2004 (UNE-EN 60300-3-2: 2008): Reliability management. Part 3-2: Application Guide. Collection of reliability data on the farm.
This section of the standard focuses on sampling and data
collection for reliability. Clear definitions of accuracy, data precision,
as well as suggested methodologies and their philosophy for obtaining the best
reliability data are well described in this section.
IEC 60300-3-3: 2017 (UNE-EN 60300-3-3: 2017 (Ratified)) : Reliability management. Part 3-3: Application Guide. Life cycle cost calculation. (Ratified by the Spanish Association for Standardization in June 2017.)
This section of the standard describes in great detail the methodology for conducting LCC studies, already discussed in other Leedeo articles, such as: Link LCC link
For the other parts of the standard, articles will be made for better understanding:
IEC 60300-3-4: 2007 (UNE-EN 60300-3-4: 2011) : Reliability management. Part 3-4: Application Guide. Guide for the specification of reliability requirements.
IEC 60300-3-5: 2001 (UNE 200001-3-5: 2002) : Reliability management. Part 3-5: Application Guide. Conditions for reliability tests and principles for conducting statistical contrasts.
IEC 60300-3-10: 2001 (UNE-IEC 60300-3-10: 2007) : Reliability management. Part 3-10: Application Guide. Maintainability. (IEC 60300-3-10: 2001)
IEC 60300-3-11: 2009 (UNE-EN 60300-3-11: 2013) : Reliability management. Part 3-11: Application Guide. Reliability-focused maintenance.
IEC 60300-3-12: 2011 (UNE-EN 60300-3-12: 2011 (Ratified)) : Reliability management. Part 3-12: Application Guide. Integrated logistics support (Ratified by AENOR in July 2011.)
IEC 60300-3-14: 2004 (UNE-EN 60300-3-14: 2007) : Reliability management. Part 3-14: Application Guide. Maintenance and maintenance logistics. (IEC 60300-3-14: 2004)
IEC 60300-3-15: 2009 (UNE-EN 60300-3-15: 2013) : Reliability management. Part 3-15: Application Guide. Systems reliability engineering.
IEC 60300-3-16: 2008 (UNE-EN 60300-3-16: 2012) : Reliability management. Part 3-16: Application Guide. Guidelines for the specification of maintenance logistics services.
At Leedeo Engineering, we are specialists in the development of RAMS projects, supporting RAM and Safety tasks at any level required, and both at the infrastructure or on-board equipment level.
Are you interested in our articles about RAMS engineering and Technology?
Sign up for our newsletter and we will keep you informed of the publication of new articles.